CNC machining, also known as Computer Numerical Control machining, has been a key element in modern manufacturing. It offers the highest level of precision uniformity, and effectiveness that wasn’t possible with traditional techniques. In automatizing the operation of machine tools through computers, CNC manufacturing allows companies to make complex pieces with remarkable accuracy. From automotive and aerospace industries to electronics and healthcare, CNC machining is utilized throughout the world to make complex components that need high precision. The integration of computers into the machining process has altered the way products are designed and constructed, setting new standards in quality and performance.
One of the major benefits of CNC machine is the ability to produce complex and intricate parts that are extremely precise. In contrast to manual machining, in which precision depends largely on the ability of the worker CNC machines adhere to programmed guidelines with a high degree of precision. Digital instructions, typically made with CAD (Computer-Aided Design) software, let manufacturers to produce parts with tolerances as tight as a couple of microns. This degree of precision is crucial in fields like aerospace and medical device manufacturing, where even small deviations could affect the efficiency or safety of a product. With CNC machining, manufacturers can ensure that every part conforms to exact specifications, which reduces chances of failure as well as the requirement for costly repair.
The efficacy of CNC machine is a key aspect in its broad adoption. The traditional machining techniques require highly skilled workers to operate the machine, change settings, and then change the tools to perform each task. This is not only long-lasting but also subject to human error. CNC machining, on contrary, can automate these processes, allowing machines to run continuously with the least amount of supervision. After a program has been set and the machine has been equipped with the material needed the machine can run multiple processes without interruptions, greatly decreasing the time to produce. CNC machines can also be capable operating continuously, which makes them perfect for big production runs. This level of efficiency enables companies to meet deadlines, enhance their output while reducing labor costs in the process, while still maintaining top quality standards.
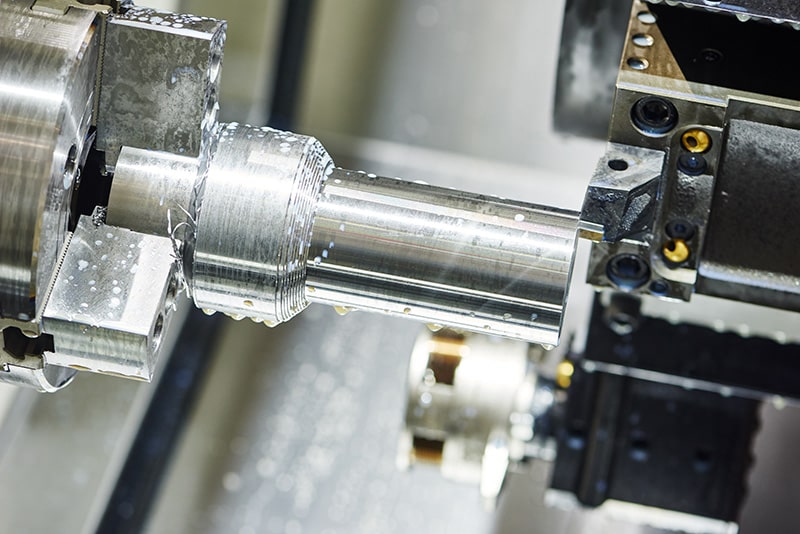
A further benefit of CNC machining services is its effectiveness. In automatizing the process of machining, manufacturers can significantly reduce the time it takes to create parts. This leads to quicker production times and cost savings. As CNC machines work continuously, with little or no supervision from a human They can boost output without losing the quality. Automation also reduces the chance of human error by ensuring that every component produced is to precisely the requirements specified within the electronic model. Further, CNC machining allows for “lights-out” manufacturing, where machines remain in operation after employees have gone home which increases productivity while decreasing labor costs.
CNC machine is also renowned for its versatility of the materials it can use. From metals like steel, aluminum, and titanium, to plastics, wood, even the composites that CNC machinery are able to be used with a range of different materials in order to make parts to be used in various applications. This versatility can make CNC machine-making suitable for a range of different industries which have their own unique material requirements. As an example, the medical industry typically needs components from biocompatible materials like titanium. The automobile industry uses tough metals like steel for engine components. However, regardless of the type of material used, CNC machines can deliver accurate cuts with consistent output, assuring that the finished product is in line with the required performance and endurance standards.
The impact on the environment of CNC operations is an additional aspect that is worth thinking about. Traditional manufacturing processes typically result in a substantial amount of waste material, CNC machines are recognized for their material efficiency. By precisely cutting and shaping material, CNC machining minimizes waste and reduces both the cost of materials and the environmental impact. In addition, automation in CNC machines helps reduce energy use in comparison to manual machining. Many modern CNC machines have been designed with sustainability in mind, employing energy efficient motors and systems to reduce the carbon footprint of their machines. This allows CNC machineries an eco-friendly solution for those who want to minimize waste and save resources.